principles in action.
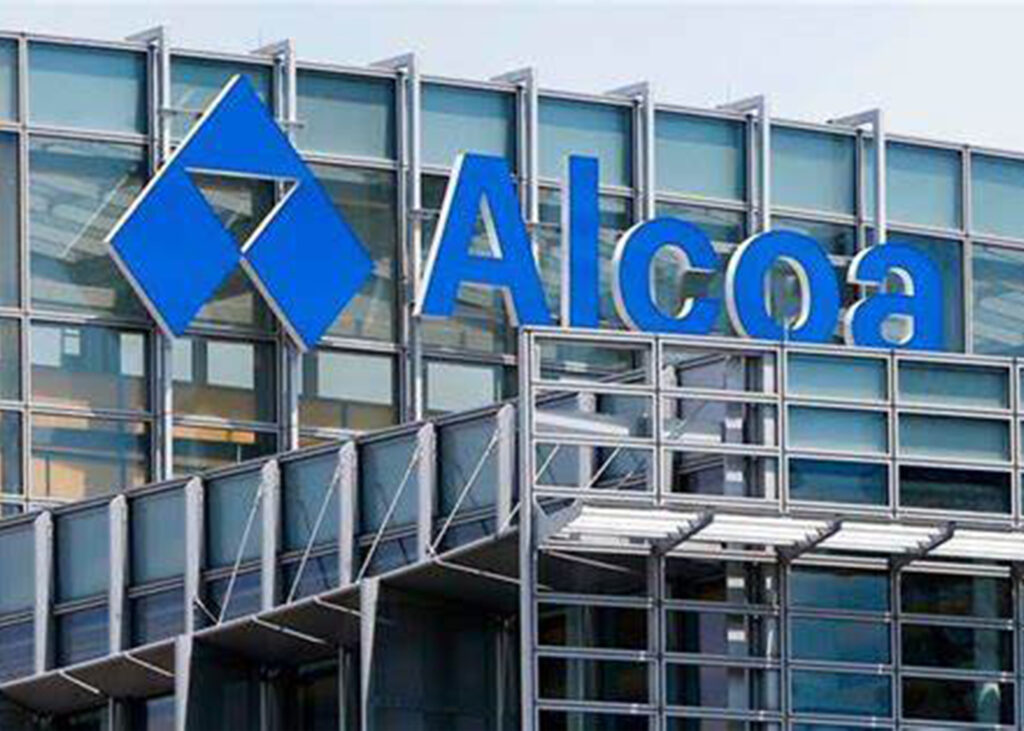
Alcoa
Safest Company
in the World
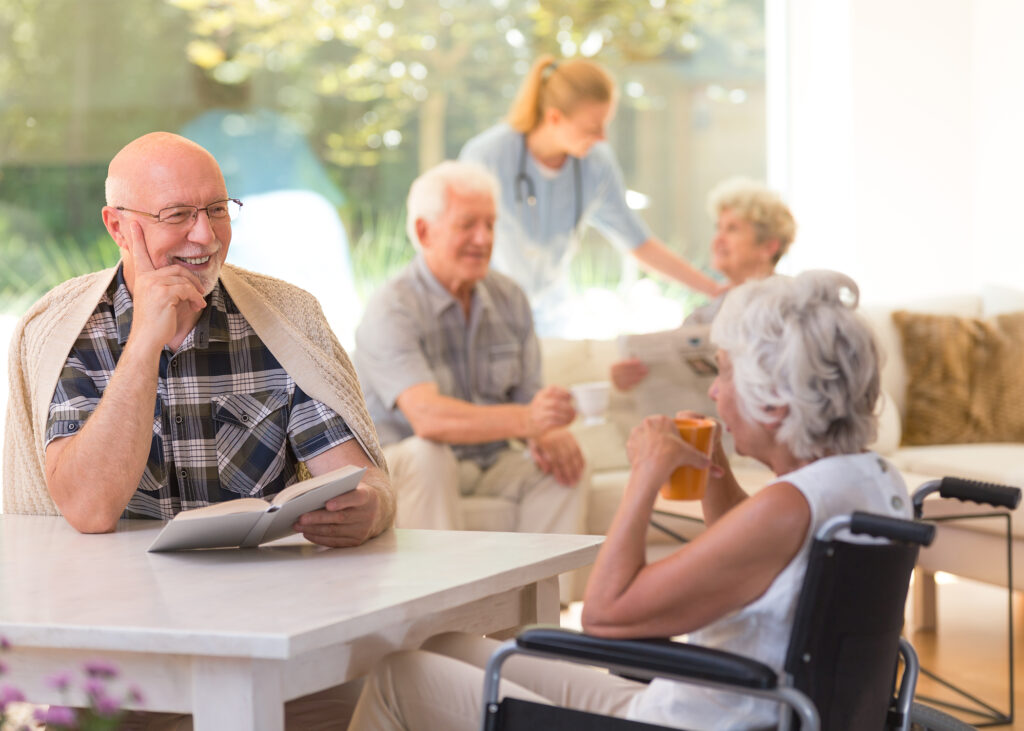
Senior Living
Making Aging
Easier
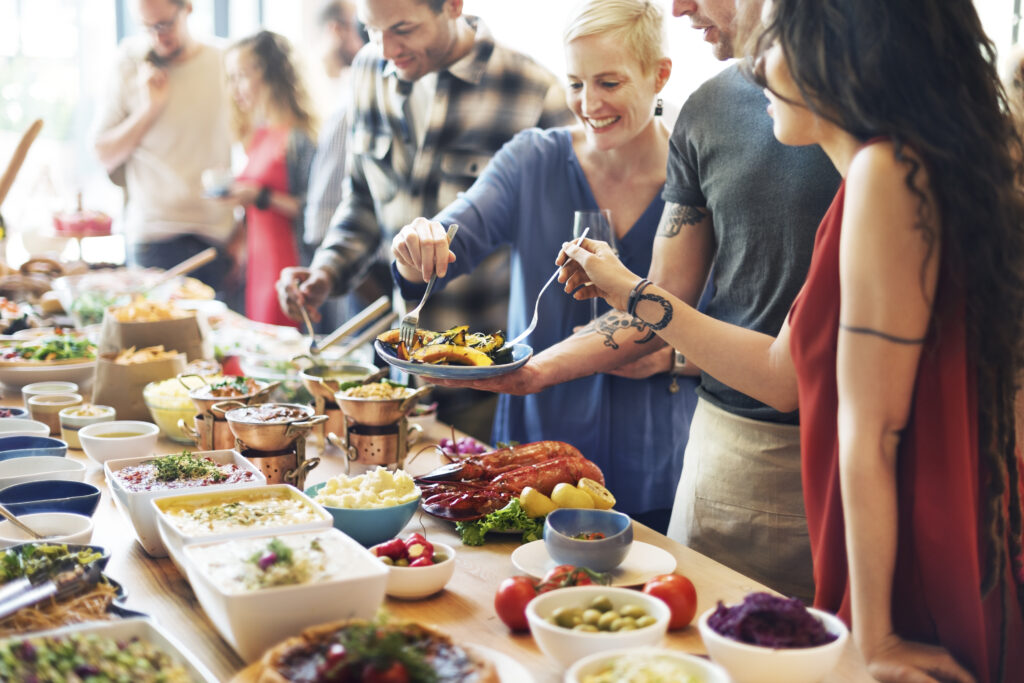
Food Ministry
Feeding 1 to 10,000
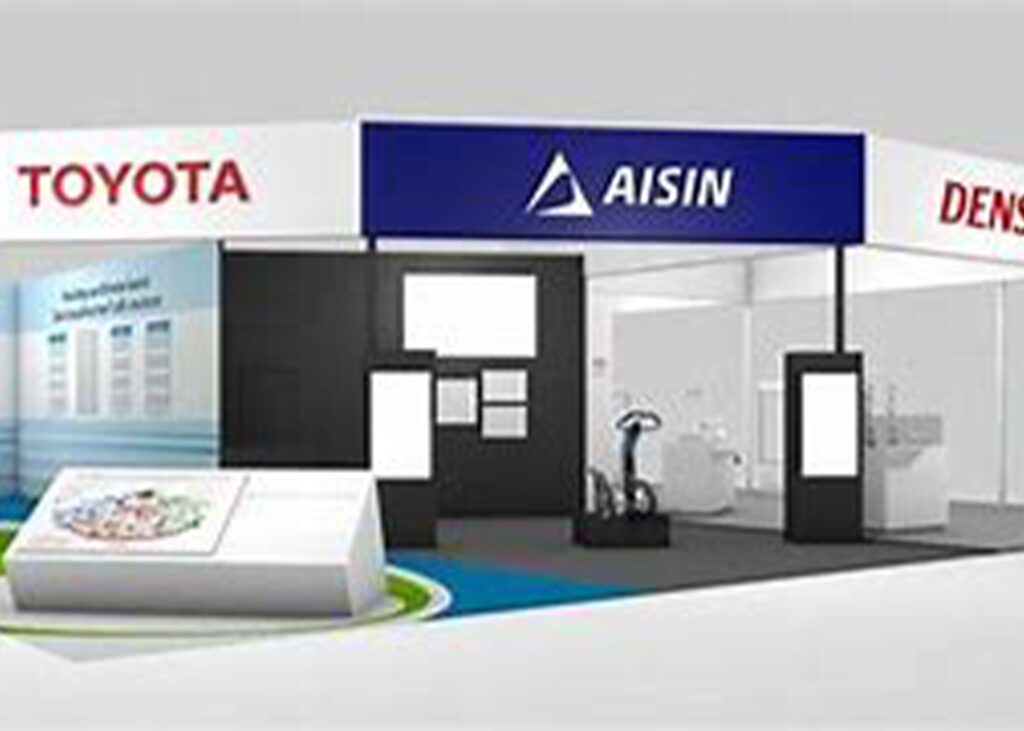
Aisin Fire
Toyota Collaboration During Crisis
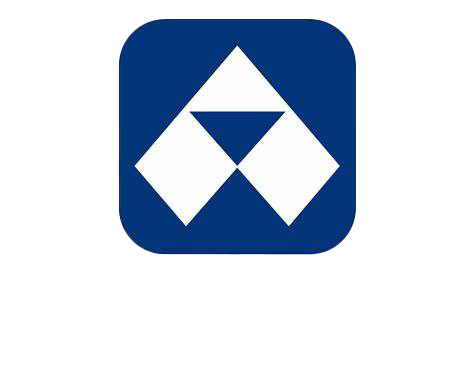
Alcoa, the World's Safest Company
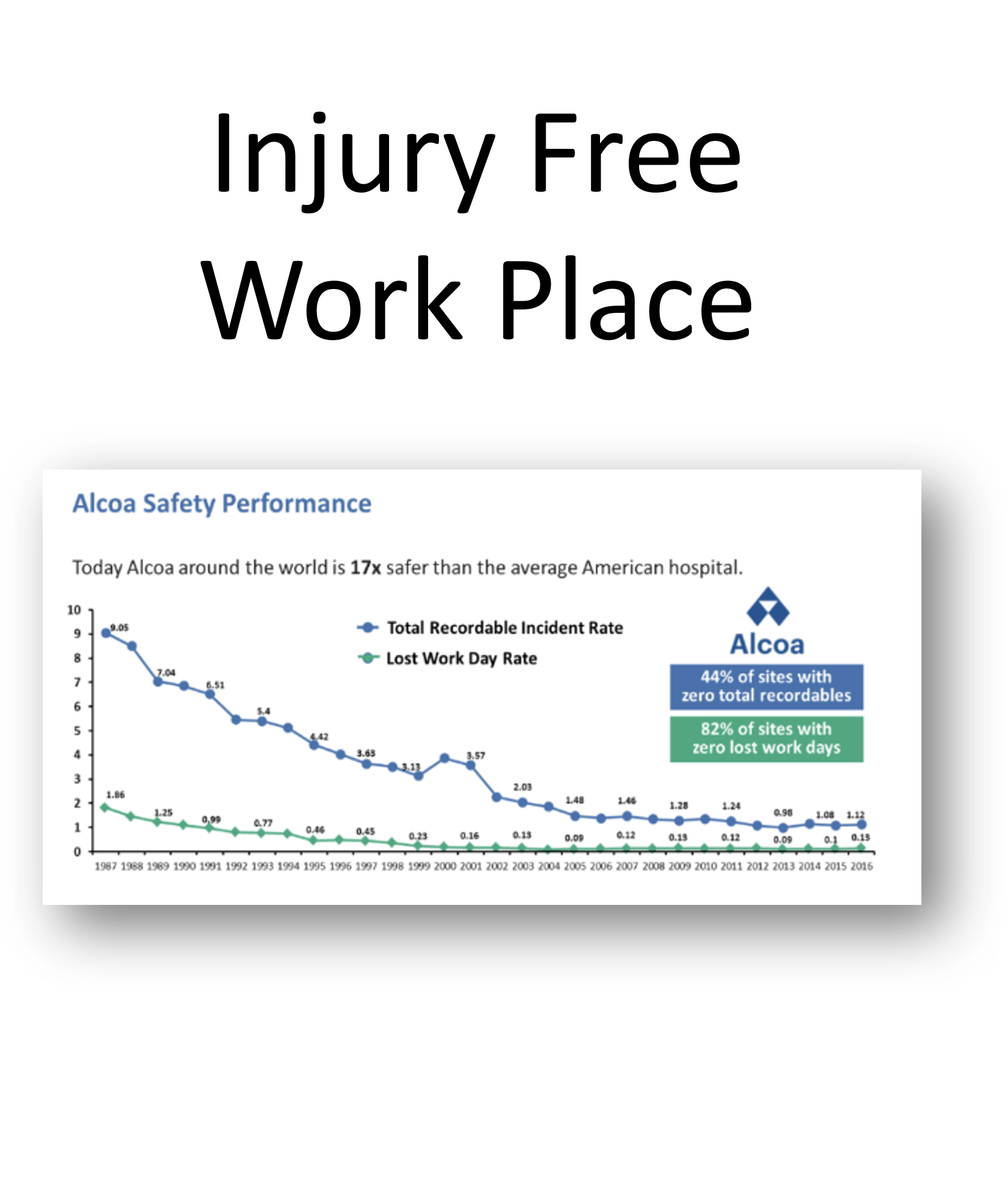
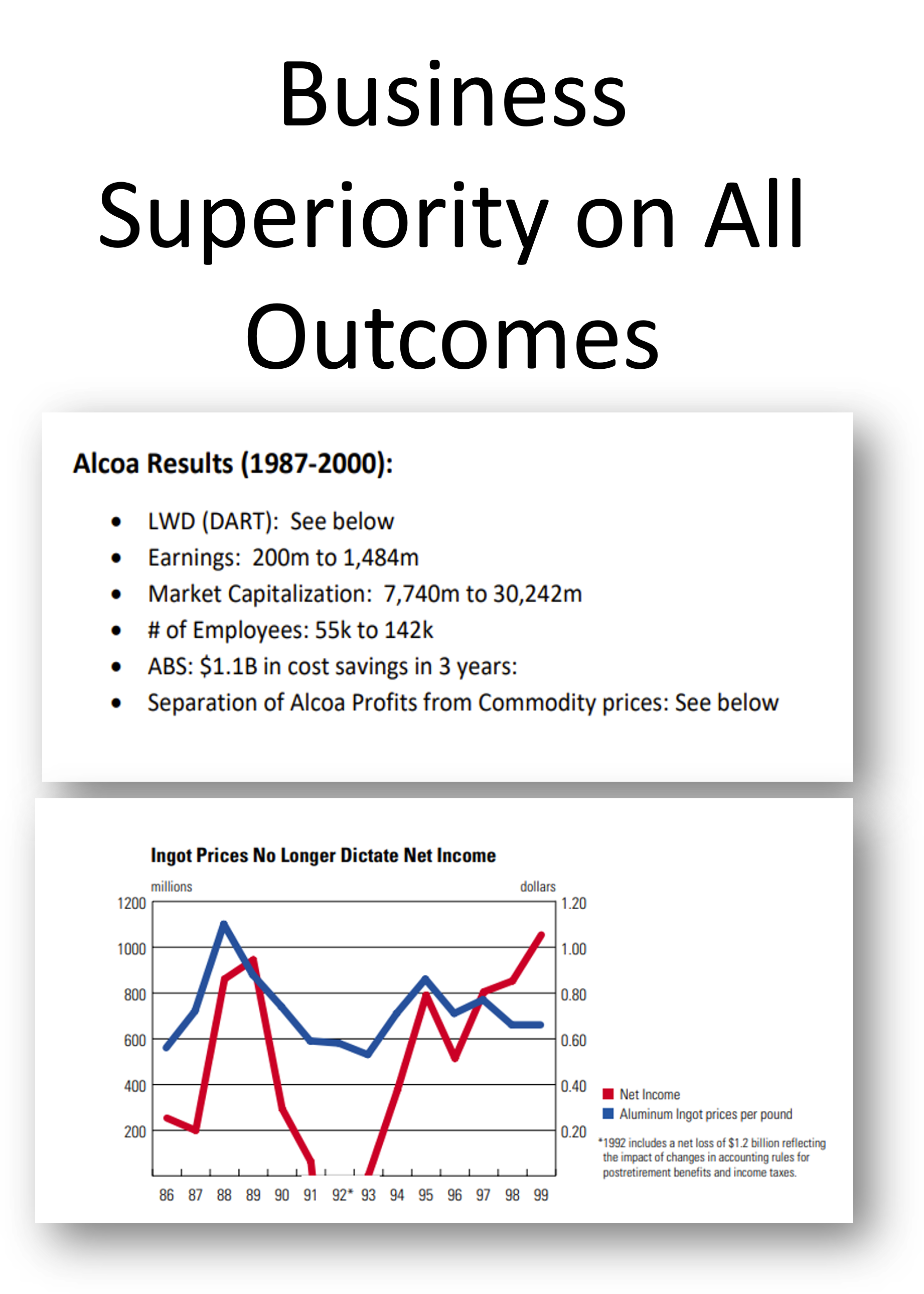
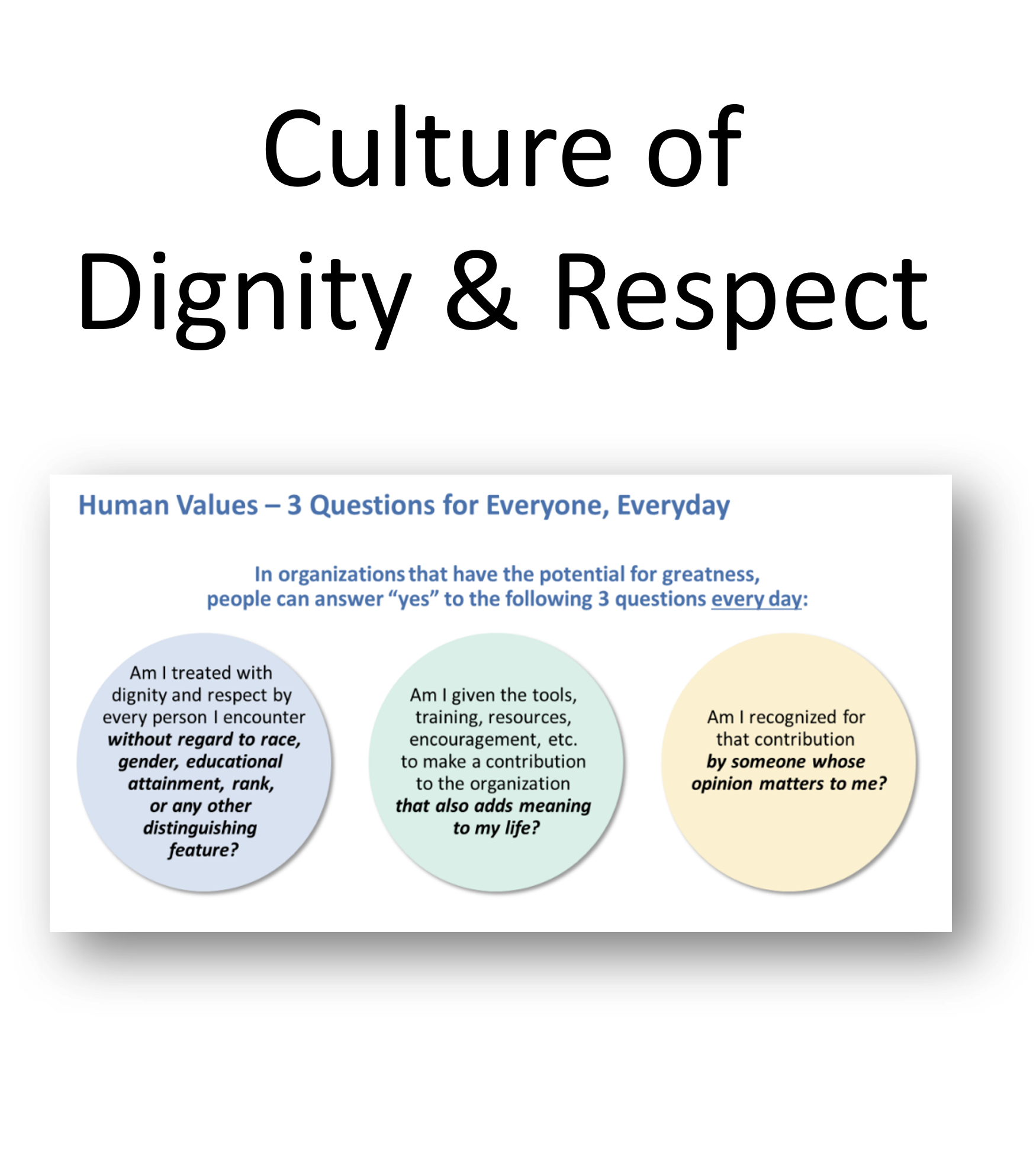
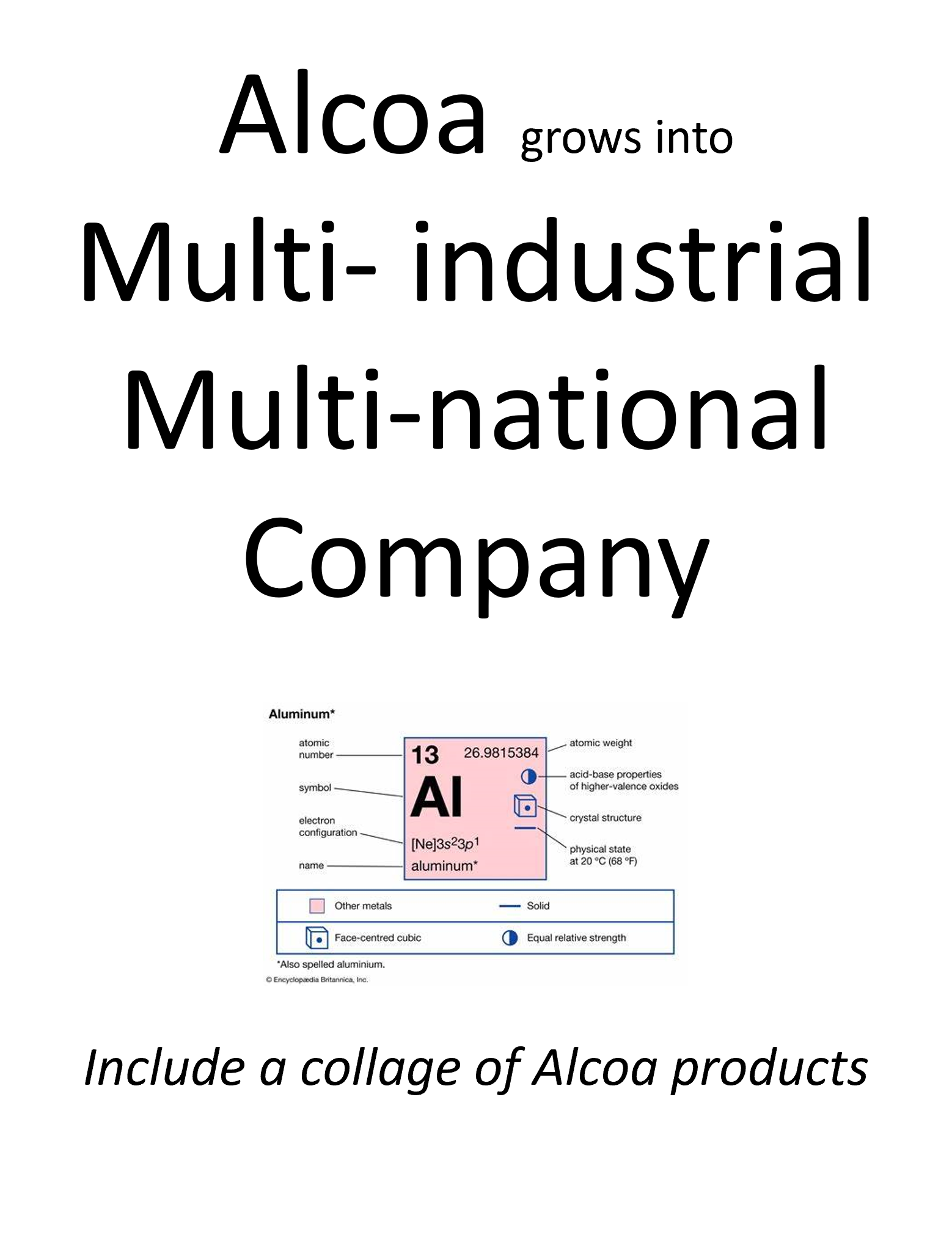
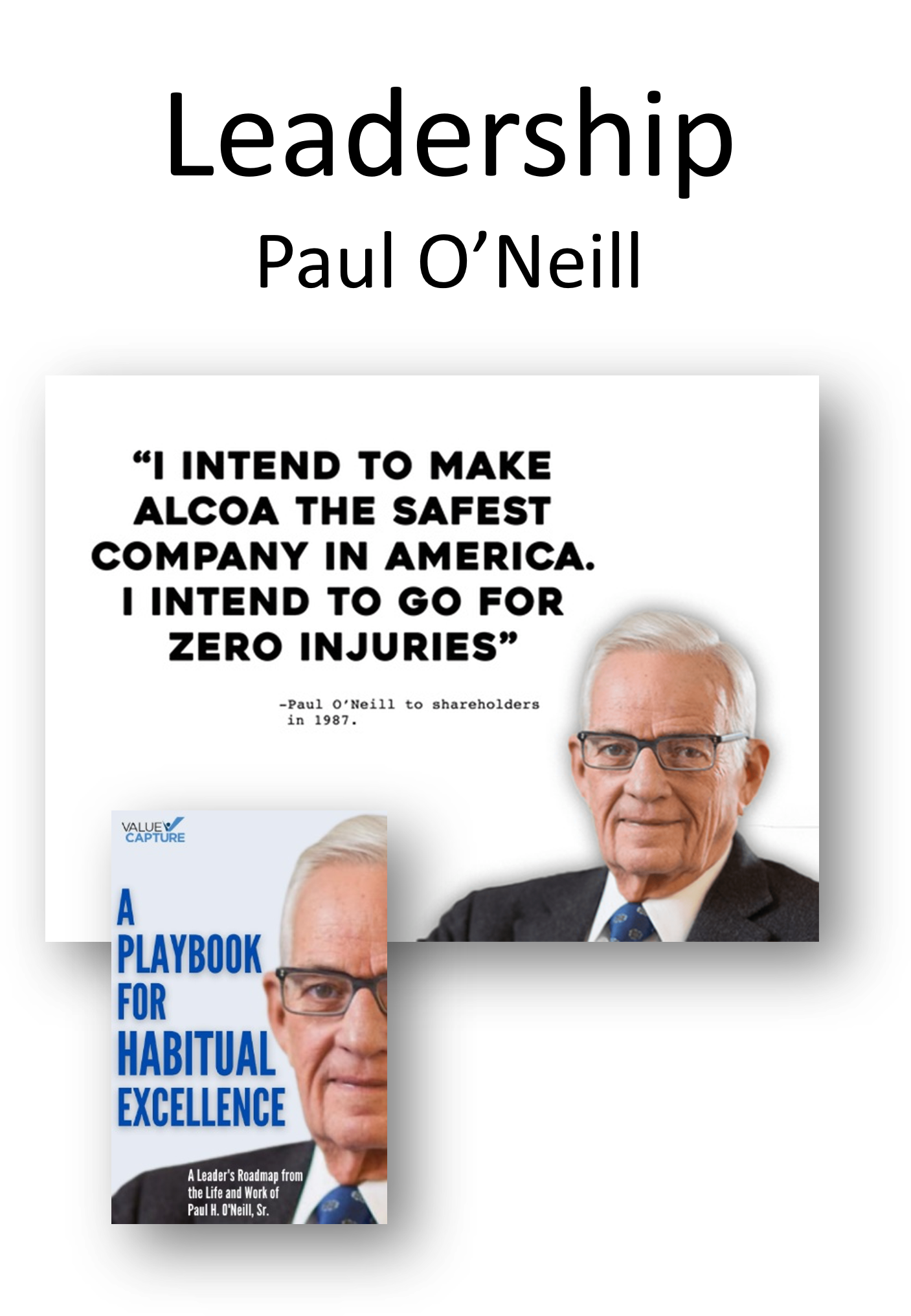
more on Alcoa.
Under the Leadership of Paul Oneill, Alcoa, a multi $billion molten metal company became the safest company in the world which then led to achieving superior results in all areas, ultimately separating company profits for ingot commodity prices.
Mr. O’Neill believed the people were the most valuable resource. He demonstrated that by making the pursuit of an injury-free workplace a precondition – that is above all goals, strategies, budgets, etc. He instituted a policy to report, mitigate, investigate, and solve all risks and injuries within 24-48 hours.
Paul O’Neill also created a world-wide information system where these incidents could be immediately reported and accessed by anyone around the world to warn of a possible risk or to proactively take corrective measures if the risk was possible in that remote area.
He later adopted the principles of the Toyota Production System as the Alcoa’s management system to establish a learning and continuous improvement culture that would sustain and continue to improve safety as well as all other business results years after his retirement.
alcoa.
how an aluminum company became the safest company in the world
TPS model area
in western pennsylvania.
making aging easier
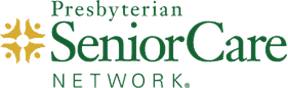
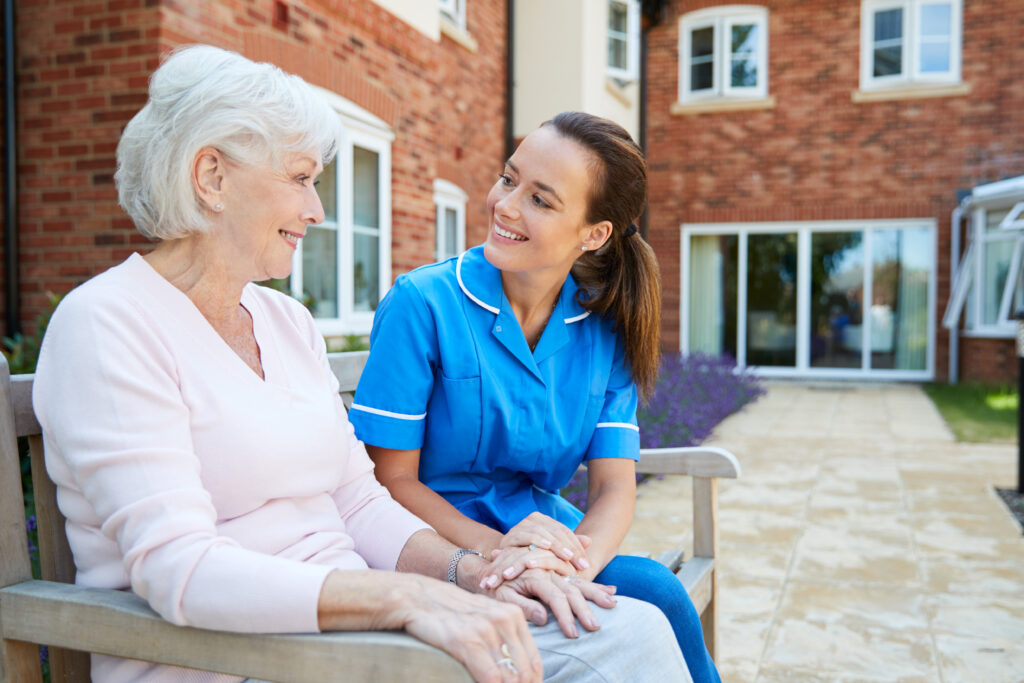
assisted living and skilled nursing.
committed to enriching the aging experience
through person-centered service and living options.
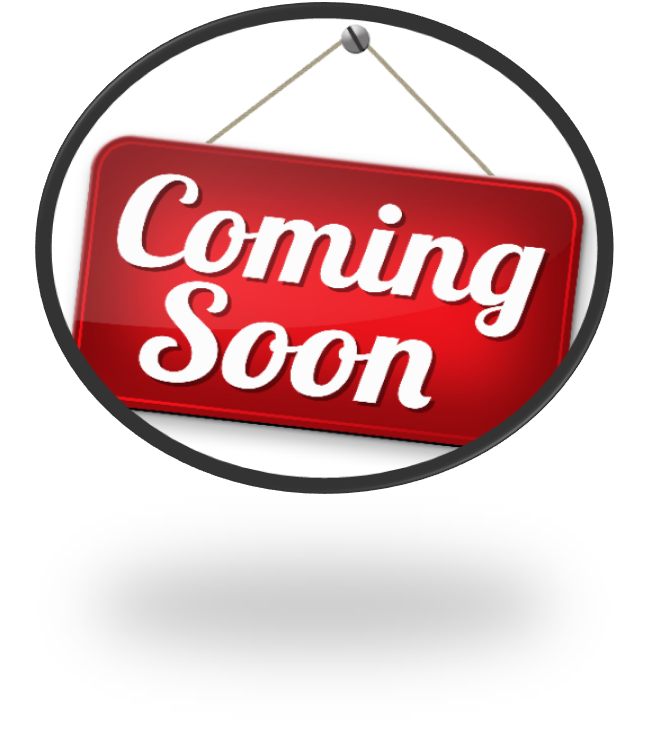
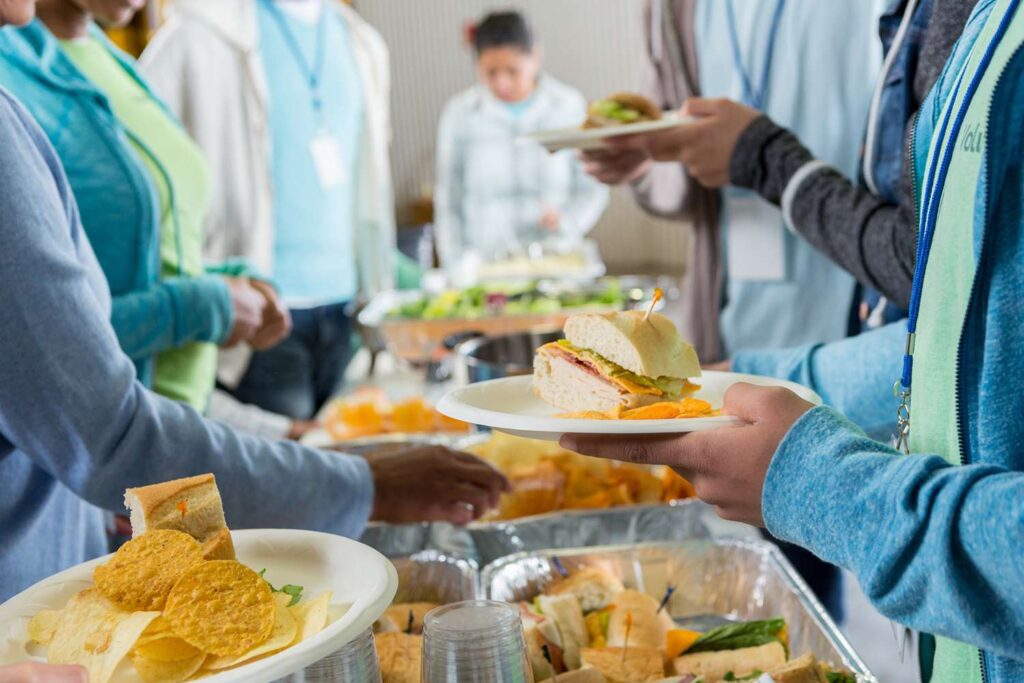
God’s Chosen People
Serving God’s Food
To God’s Family
captured in Keith and Sally Turnbull’s book…
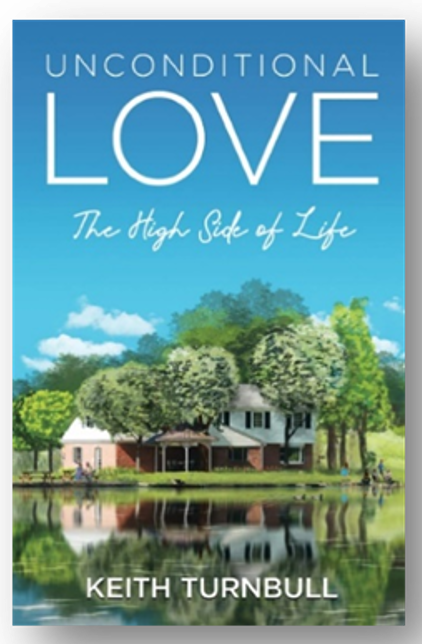
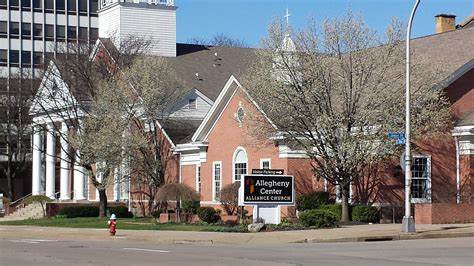
more on the food ministry.
Excerpt from Keith Turnbull’s book: Unconditional Love: The High Side of Life…
The Food Ministry is so robust and capable that it stepped into the gap for inner city children when COVID-19 struck in 2020. Drive-through free warm lunches were first, followed by delivery to home via Urban Impact Foundation. Then, they doubled up to warm lunch plus tomorrow’s breakfast given to each child. How many? More than 1,000 meals per day. Why? Because that is how God’s Chosen People Serve God’s Food to God’s Family.
Is it hard to do? No! Because CONTINUOUS Flow is SCALABLE and ROBUST, capable of serving one person or 10,000.
But the message to you from the case study is that you can apply the Principles to your life, your family, your church, your work or your neighborhood by using each step we used for food.
Converting each step from food to family, it would be:
• Who are your CUSTOMERS and what are their needs and wants?
• What TASKS are you doing to meet these needs and are you doing them well?
• Are you using TEAMWORK and are you mentoring each other?
• Do your processes FLOW and are they connected in ways that are kind and enabling?
• Do you INVENTORY wisely and is it supportive of the prior four questions?
• Do you solve PROBLEMS with kind mentoring and Problem/Cause/Solution/Action/Measure?
• Is YOUR FLOW balanced and constructive for your family?
• Is YOUR MENU for life proper and are you living it right?
• Is your MENU CONNECTED such that your family thrives?
• Is your SUMMARY that YOU are doing these 9?
Are you willing to put God in all 10 of these? We did and found Him to be an awesome traveling partner. Joe and Richard did and found that they could feed 1,000 people, approaching the 5,000 Jesus fed in Matthew 14:13-21.
community church food ministry
subheading
aisin seiki plant fire and toyota.
subheading
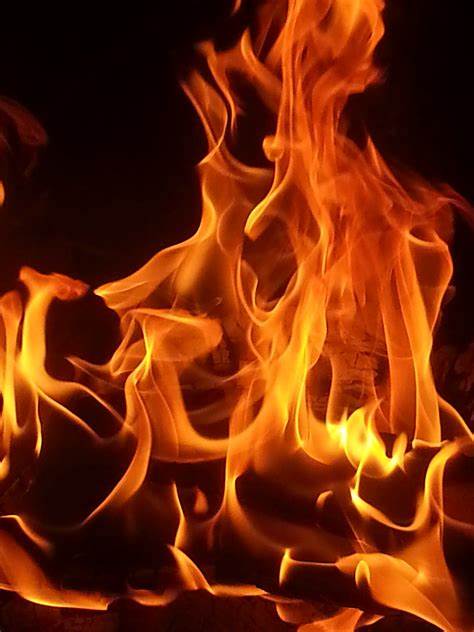
recognizing and responding to small changes repeatedly, continually develops work force strength to respond quickly to a crisis.
p-valve.
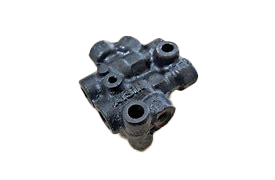
self-organization
in
chaos.
On February 1, 1997, a fire destroyed the Aisin Factory where the P-value, a proprietary and essential brake part was used in all Toyota vehicles worldwide at the at time (32,500 per day).
200 suppliers self-organized to get P-valve production started within 2 days
63 different firms took responsibility for making the parts piecing together what existed of engineering documents, using some of their own equipment, rigging together temporary lines to make the parts, and keeping Toyota in business almost seamlessly.
This paper captures the unmatched agility and adaptability Toyota has developed that enables both them and their network partners to be capable of responding uncommonly well to small problems on the shop floor to crises threatening the full stop of production and the loss of profit in the $billions.
What complex problems can we partner with you to solve?
We tailor our offerings to meet your unique needs.
Reach out to our team to start a conversation.